Naar een hoger applicatierendement
Voor geïntegreerde lakkerijen hebben we een unieke methodologie uitgewerkt om het poedercoating proces in kaart te brengen en te optimaliseren. In drie stappen kunnen we samen evolueren naar een hoger applicatierendement. Meer weten over onze aanpak of wil je meteen aan de slag? Vraag vandaag nog een audit.
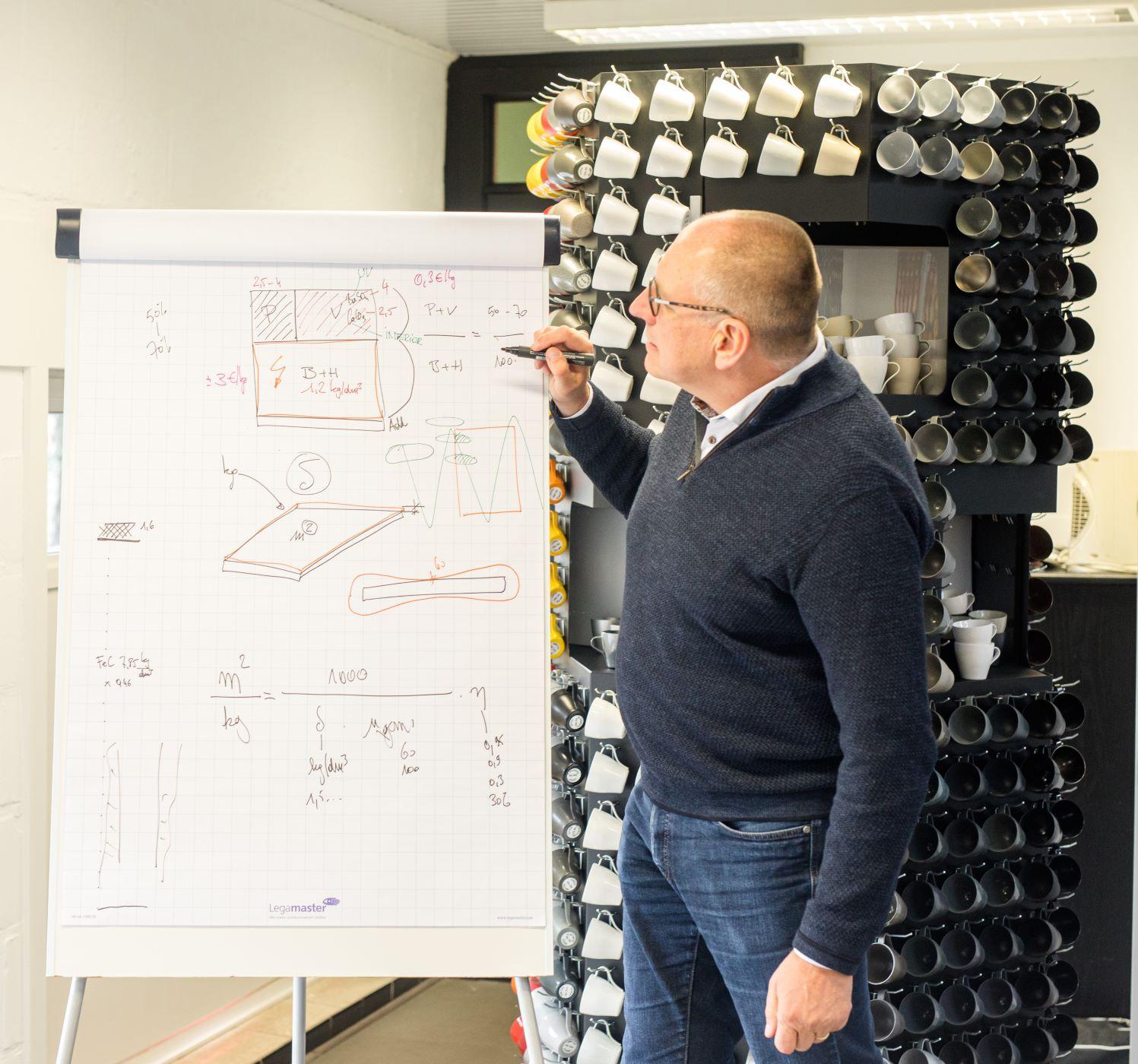
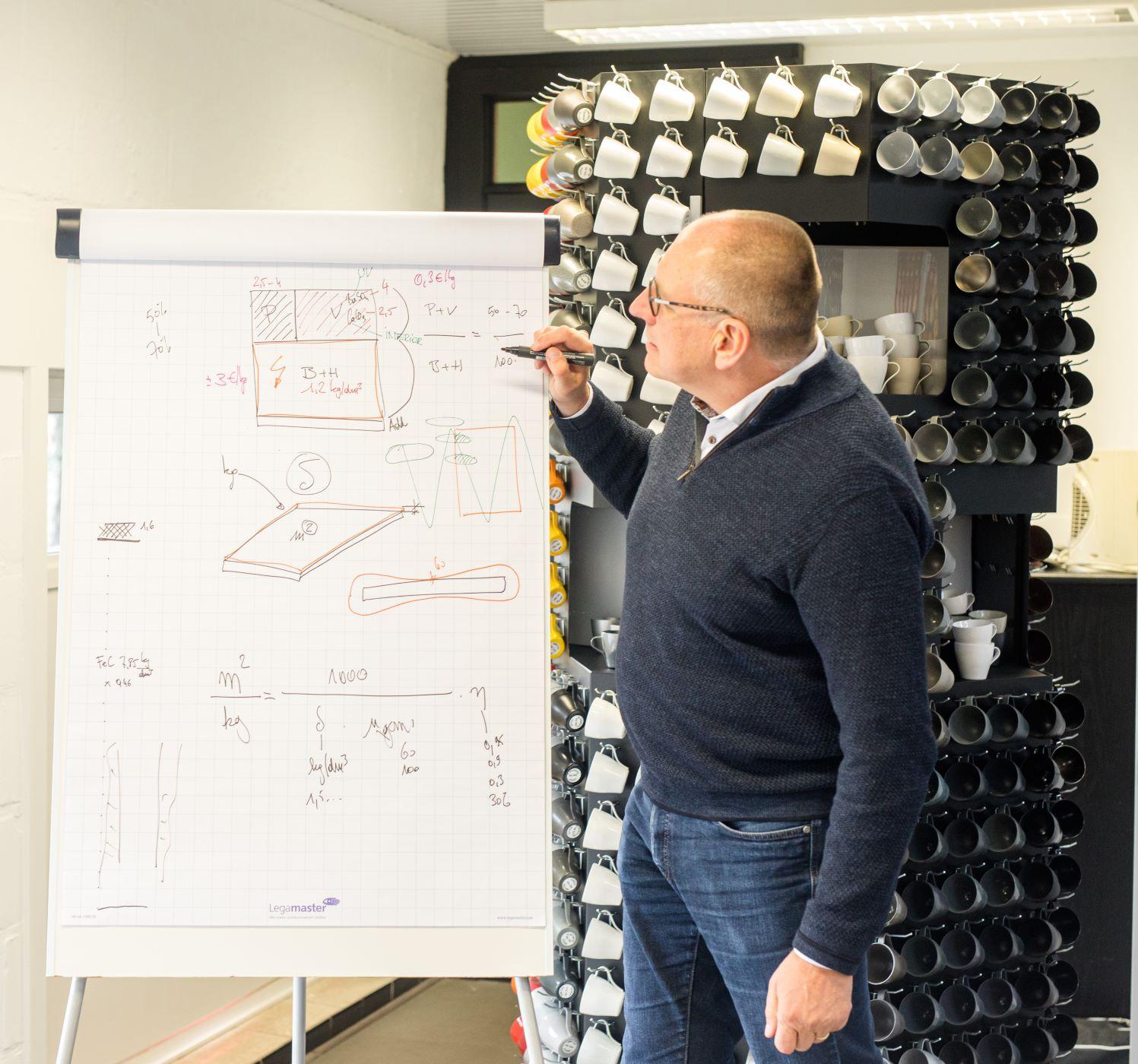
De HaTwee methodiek
Benieuwd hoe wij jouw productieproces kunnen optimaliseren?
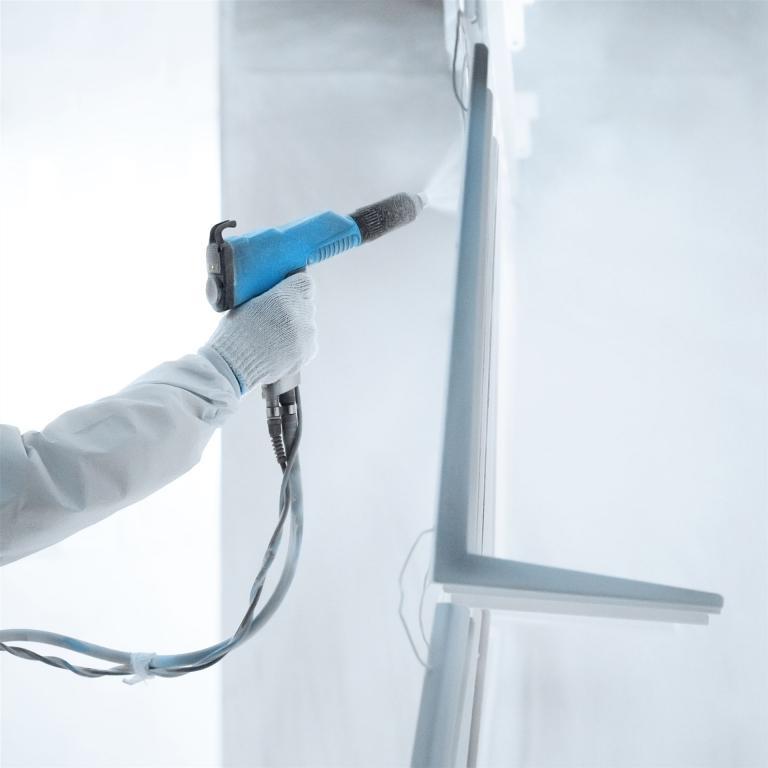